Coupling of Microscopy and Thermomechanical Models to Explain the Extent and Location of TRIP Product in Simulated PBF-LB of Ti-1023
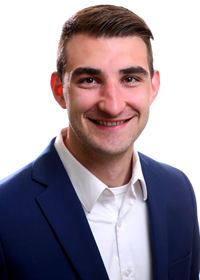
Metallic additive manufacturing (AM) has widely expanded in use. As a result, so too has the need for alloys tailored to the unique processing conditions experienced during AM. Widely used titanium (Ti) alloys, such as Ti-6Al-4V (wt.%), were initially chosen by the aerospace and defense sectors for AM. However, non-equilibrium conditions like rapid cooling inherent to AM have presented difficulties in producing high strength, high quality (i.e. crack-free) AM builds with traditional alloys. Another subset of Ti alloys, β-Ti, can mitigate these issues by undergoing a solid-state phase transformation to better accommodate residual stresses/strains that develop and lead to cracking. This mechanism is referred to as transformation induced plasticity (TRIP). Compared to conventional deformation via slip, TRIP in β-Ti alloys may result in better combinations of strength and ductility. To better understand what controls and affects TRIP behavior during AM, simulated powder bed fusion-laser beam (PBF-LB) was performed on the β-Ti alloy Ti-10V-2Fe-3Al (wt.%) (Ti-1023) during synchrotron-x-ray imaging at the Advanced Photon Source at Argonne National Laboratory under varying processing conditions. TRIP product was observed for all conditions to various extents and locations. Local strains and microscopic grain characteristics were identified as the two main factors controlling the TRIP behavior of this alloy during AM. The findings of this work provide greater insight into TRIP of the metastable β-phase at the melt pool level for Ti-1023 and the formation of unique microstructures in the solid state relevant to full AM builds.